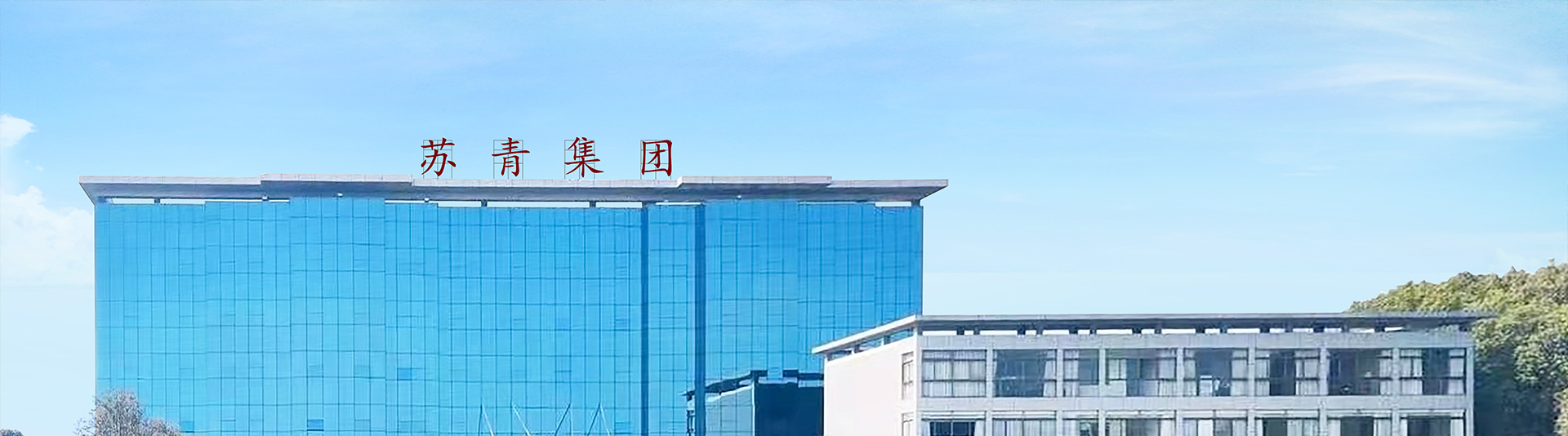
Application of Suqing Brand D002 Resin on MTBE
1、 Application of D002 catalyst resin on MTBE
Suqing brand D002 catalyst resin is a specialized catalyst used in the etherification reaction of MTBE production. In order to ensure its normal use, the correct loading and usage methods are introduced as follows:
1. Resin filling:
1.1 Preparation work:
1.1.1. Contact professional maintenance personnel to open the reactor manhole and purifier manhole;
1.1.2. Contact the laboratory personnel to sample the oxygen content during the analysis period, and require an oxygen content of ≥ 20% (V) before entering the operation;
1.1.3 Thoroughly clean the mechanical impurities, possible oil stains, rust, etc. inside the reactor and purifier to ensure that these hidden dangers do not cause damage to the resin. Thoroughly flush the pipes that have been fed. Washing water requires deionized water, and if necessary, wipe the walls clean with a cloth;
1.1.4. Carefully inspect the internal components of the reactor, especially the fixation of the resin filled grille and whether the stainless steel wire mesh is damaged (the wire mesh should be in three layers, with 80 mesh in the middle layer and 20 mesh in the upper and lower layers). The periphery of the wire mesh should be compacted with original circular stainless steel flat strips, and fixed to the support ring with screws and the support grille, The excess area around the three layer wire mesh should be pressed into the gaps between the grid and the reactor wall using a flat shovel, and all gaps should be filled with asbestos or 80 mesh wire mesh to ensure that the catalyst does not leak. Generally, a 200mm thick layer is laid on the wire mesh φ 2-5mm thick quartz sand (before filling this quartz sand, ensure that the content of SiO2 is greater than 99%, soak it in 10% hydrochloric acid solution for 8 hours, and then rinse it with deionized water for filling). After leveling, catalyst can be loaded into the reactor.
1.1.5. Transport the tools for filling resin to the site, and all tools must be cleaned with deionized water before use;
1.2. Resin filling:
1.2.1 Fill the purifier and reactor with resin according to the design amount (note that appropriate expansion space should be left), and handle it gently during the filling process to prevent stepping on the resin. Usually, the next person goes to the bottom of the reactor and uses a long canvas bag to place it from the top of the reactor. The catalyst flows along the bag to the bottom of the reactor. After most of the catalyst is added, the personnel inside the reactor can withdraw. After the remaining catalyst is added, the surface should be smoothed and all flanges should be sealed.
1.2.2. When loading catalyst resin, it is necessary to strictly prevent prolonged contact with metals and water (especially iron and non deionized water), otherwise the activity of the catalyst in contact will be affected. Filling should be done on sunny days;
1.2.3. After filling, the number of tools and bags should be counted, and they should not be left in the reactor, and a dedicated person should be assigned to take charge;
2. Soaking of D002 catalyst resin with methanol (i.e. pre-treatment):
2.1. For ease of preservation, D002 contains about 50% water. Before the etherification reaction, in order to prevent this water from reacting with isobutene in C4 to generate tert butanol, which affects the purity of MTBE, it is necessary to replace this water (in addition, excessive water in the resin may cause a sharp increase in pressure difference due to its immiscibility with C4). The method of replacing water is to use a circulating pump to extract methanol from the bottom of the reactor, After passing through the booster pump, enter from the upper part of the reactor and circulate for 15-24 hours.
2.2. Due to the fact that 20% methanol solution can dissolve with C4, it is generally considered appropriate to reduce the water content in the catalyst to around 15%. Based on this calculation, using twice the total amount of resin water in methanol for circulation can reduce the water content of the catalyst to a suitable range.
2.3. Determination of water content in catalyst resin after methanol immersion: If the mixture is uniform and does not generate bias flow, the water content in circulating methanol is basically the same as that in catalyst micropores. Therefore, analyzing the water content in circulating methanol represents the water content in the catalyst.
3. Reasons for the decrease in resin activity of D002 catalyst:
The main reasons for the decrease in catalyst activity are as follows:
3.1. Cation content in the feed liquid: As D002 catalyst is a strong acidic cation exchanger, it has good selectivity for all common cations (such as calcium, magnesium, sodium, potassium, iron, etc.). Therefore, when these ions are contained in the feed liquid or artificially introduced, they will be quickly replaced by H+in the catalyst, thereby reducing the activity of the resin. This is the most common and major cause of catalyst deactivation. Generally, a protective purification bed can be used for removal.
3.2. Weakly alkaline organic nitrides in the feed liquid: These nitrides (such as organic amines, etc.) are difficult to remove from the protective bed, and their damage to the resin is also difficult to recover. They should be controlled in the feed liquid;
3.3. Excessive temperature in the etherification reaction leads to the detachment of sulfonic groups and a decrease in activity. This decrease in activity is also irreversible.
3.4. The micropores of the catalyst are blocked by fine impurities, preventing the material from entering the micropores and contacting H+, resulting in a decrease in activity. In this case, as long as the pore size is dredged through appropriate methods, its activity can be restored.
4. Special note: When the catalyst provided is on a wet basis (i.e. containing about 50% water), the volume of methanol remains basically unchanged after dissolution. (However, if the filling process takes too long and the packaging is damaged, there may be a slight loss of water inside the pores of a few resins, leaving about 3% expansion space) At this time, its expansion space may not be considered; When the catalyst provided is on a dry basis, 50% expansion space should be considered during loading.