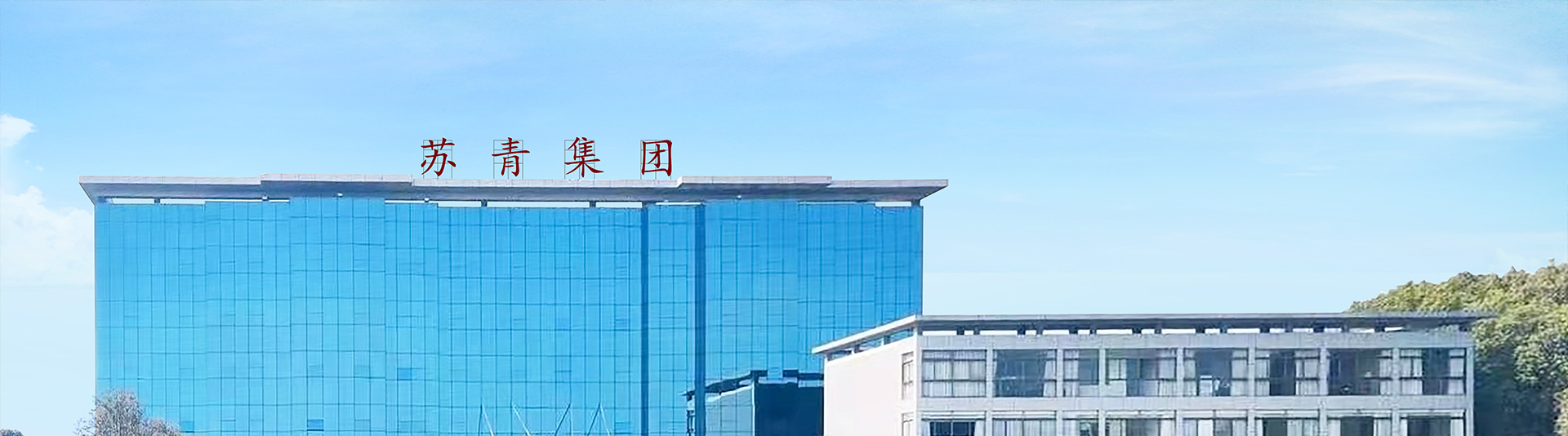
Explanation of oxidation and degradation of ion exchange resins
Ion exchange resins are a type of insoluble organic synthetic materials that are insoluble in water and organic solvents, as well as in acids and alkalis. Its heat resistance and chemical stability are also similar to other types of organic synthetic materials. The heat resistance of ion exchange resins refers to the impact of the environmental temperature of the resin on its quality and service life. The chemical stability of ion exchange resin refers to the influence of water, organic solvents, acids and alkalis, and oxidants on the quality and service life of the resin.
1、 The effect of water and organic solvents on resins:
Ion exchange resins are insoluble in water and any other organic solvents, but water and organic solvents have a certain degree of swelling on the resin, and the degree of swelling also varies depending on the organic solvent.
A common situation is that resin loses water due to prolonged or improper storage. When the water loss is severe, if the resin is directly immersed in water, it may rupture due to the rapid expansion of the resin by water, which affects the strength of the resin. Especially for gel resin. In this case, the resin needs to be immersed in a NaCl solution of more than 15% for several hours first. After the resin is completely soaked, rinse off the salt water with water.
If it is necessary to frequently alternate the treatment of resin with aqueous solution and organic solvent, the resin may often experience volume shrinkage and expansion, resulting in resin fragmentation. Therefore, special attention should also be paid to the speed of the alternating treatment.
2、 The impact of environment, usage temperature, and acidity on the resin:
As the environment and usage temperature increase, the functional groups of ion exchange resins may detach, thereby reducing the exchange capacity of the resin. In the presence of acids or bases, the detachment rate of functional groups in the resin may accelerate. Due to the different types and matrices of ion exchange resins, their thermal stability varies. But overall, the higher the crosslinking degree of the resin, the poorer its thermal stability.
1. Styrene based strongly acidic and acrylic based weakly acidic cation exchange resins: These two types of resins have good temperature resistance and stability. Their H-type resins can be used at 100 ℃, while Na type resins can be used at 120 ℃. It can meet the requirements of general water treatment and many other applications. But for some special purposes, such as olefin hydration catalysts, which require high temperatures of around 150 ℃, special temperature resistant resins are required. For example, D002-II heat-resistant cationic catalytic resin can be used for a long time at 170 ℃ without shedding exchange groups.
2. Styrene based strong base type I anion exchange resin: This type of resin has a maximum operating temperature of 80 ℃ for Cl type and 60 ℃ for OH type. The main reason for this type of resin is that its functional group quaternary ammonium salt decomposes at higher temperatures, thereby reducing its exchange capacity.
3. Styrene based strong base II type anion exchange resin: This type of resin has an ethanol group in its functional group quaternary ammonium salt, which makes it degrade faster at higher temperatures than I-type strong base resin, and its temperature resistance is also worse. The maximum usage temperature of Cl type resin is 60 ℃, and the maximum usage temperature of OH type resin is 40 ℃.
4. Acrylic acid is strong base and weak base anion exchange resin: this kind of resin, because its exchange group is connected to the resin skeleton through the amide bond, and the chemical stability of the amide bond is much lower than that of the C-C bond. Therefore, the chemical stability of this kind of resin is poor. In the presence of acids and bases, it can accelerate the decomposition of amide bonds, resulting in lower stability. Therefore, when using this type of resin, not only should the temperature be controlled, but when treating or regenerating the resin with acid and alkali, the temperature of the acid and alkali should also be controlled at a lower level. Generally, the use and regeneration temperature of acrylic strong alkali resins should not exceed 30 ℃, and the use and regeneration temperature of weak alkali resins should not exceed 45 ℃.
3、 The effect of oxidants on resins:
When ion exchange resins encounter strong oxidants, they will be oxidized, resulting in a decrease in the strength and exchange capacity of the resin, thereby affecting its service life. There are many types of strong oxidizing agents, but the main ones often encountered during the use of resins are free chlorine and dissolved oxygen in water. From past experience, dissolved oxygen in water does not have a significant impact on resin oxidation and has a relatively small impact. And free chlorine has a strong ability to oxidize and destroy the resin, which has a significant impact.
The sources of free chlorine mainly come from two aspects: residual free chlorine from disinfection treatment of raw water or materials; Free chlorine brought in by poor quality hydrochloric acid used for resin regeneration or treatment (some industrial by-products contain high levels of free chlorine).
The effect of free chlorine on resin varies depending on the anion resin and cation resin: for cation resin, the functional groups of the resin are relatively stable, and free chlorine mainly oxidizes and degrades the skeleton of the cation resin, thereby increasing its moisture content and decreasing its strength. The color of the visible resin has faded on the appearance. For anion resins, as amines or ammonium are more easily oxidized, free chlorine will first oxidize and destroy the exchange groups of the anion resin, resulting in a decrease in the exchange capacity of the resin. If the amount of free chlorine is high, it will further oxidize and damage the resin skeleton, resulting in a decrease in resin strength.
However, in practical applications, due to the fact that the cation resin is generally placed in front of the anion resin and the content of free chlorine is generally low, the possibility of oxidation attack on the cation resin is much greater than that on the anion resin.
After the resin is oxidized, not only does it decrease in quality and shorten its service life, but sometimes it also affects the quality of the effluent or treated materials. Therefore, it should be avoided as much as possible, as follows:
Try to use high-quality hydrochloric acid as much as possible to avoid introducing free chlorine from hydrochloric acid;
Use activated carbon to treat water or materials containing free chlorine before contacting the resin. The use of granular activated carbon adsorption columns before ion exchange resins can not only adsorb organic matter and reduce the chances of contamination, but also effectively remove free chlorine, providing dual protection for the resin;
The higher the crosslinking degree of the resin, the stronger its oxidation resistance. If it is known that the system inevitably contains free chlorine, it is recommended to use macroporous ion exchange resins. Because macroporous resins generally have a higher degree of crosslinking and stronger antioxidant capacity.